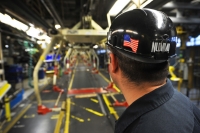
End of the line for NUMMI
I just listened to the recent “This American Life” podcast* that explored the rise and fall of the NUMMI auto assembly plant in Fremont, California and what it says about the auto industry. (In 1984, the then-dominant General Motors and the insurgent Toyota agreed to build cars together: Toyota would learn to adapt its renowned manufacturing/management/teamwork system to the American context and GM would learn how that system had allowed Toyota to efficiently build very high quality vehicles.)
I immediately recognized that the story had implications for education reform. So did John Thompson, commenting on the This Week in Education blog. In the podcast we learn that at Toyota plants the workers are organized in teams and each member bears the responsibility for quality. Team members are well-trained in the assembly process, each step of which is timed down to the second. We also learn that it took a visionary United Auto Workers leader to get his rank-and-file members to go along with the changes, which required that they give up seniority and work closely with managers in an atmosphere of trust.
Thompson thinks the lesson is that schools should give teachers more autonomy and independence. But I thought the lesson was that teachers should recognize that they are part of a team, that they all are responsible for making sure kids learn, and that union leaders should be more cooperative and work more closely with principals and superintendents and not negotiate down to the minute how long they are required to be at school. This goes both ways, of course. Trust is like that.
— Richard Lee Colvin
*You can download the podcast for free from iTunes or for 99 cents from the This American Life home page. You can also read an All Things Considered story about the plant’s history from back in March.